Thames Tideway Tunnel Project
The Challenge
The Thames Tideway Tunnel was a critical project designed to protect the tidal River Thames from increasing pollution, as London’s outdated sewerage system discharges millions of tonnes of untreated sewage mixed with rainwater into the river annually. The tunnel spans approximately 31km, can be more than 7m wide and 68m deep. To mitigate health and safety risks during inspections, Tideway sought to employ robots, necessitating the development of a robot capable of meeting specific requirements.
The main tunnel imposes challenging demands on the robotic inspection system, including the ability to traverse 7km within an 8-hour window, identify a range of defects in the extensive tunnels and shafts, and achieve detection accuracy within +/- 0.5m. Following a global search, it was concluded that a custom solution would be needed to fulfill these requirements.

The Solution
Building on our extensive experience in autonomous infrastructure inspections, the team of robotics, computer vision, and machine learning engineers developed the ATARI (Abyss Tunnel and Aqueduct Robotic Inspector). Equipped with six computer vision cameras, four strobe lights, two lidar scanners, and various other sensors, the ATARI can travel autonomously, capturing brightly illuminated, 360-degree images of the tunnel interior. It can operate continuously along a 10km tunnel and be launched and retrieved via drop shafts, eliminating the need for personnel to enter the confined space.
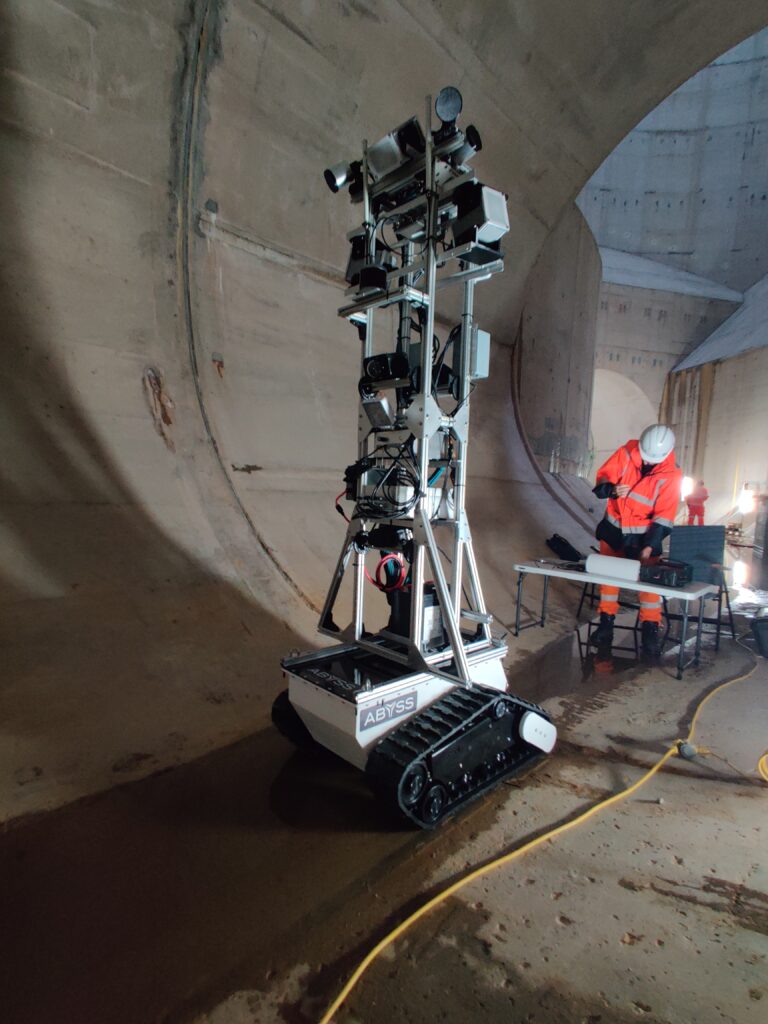
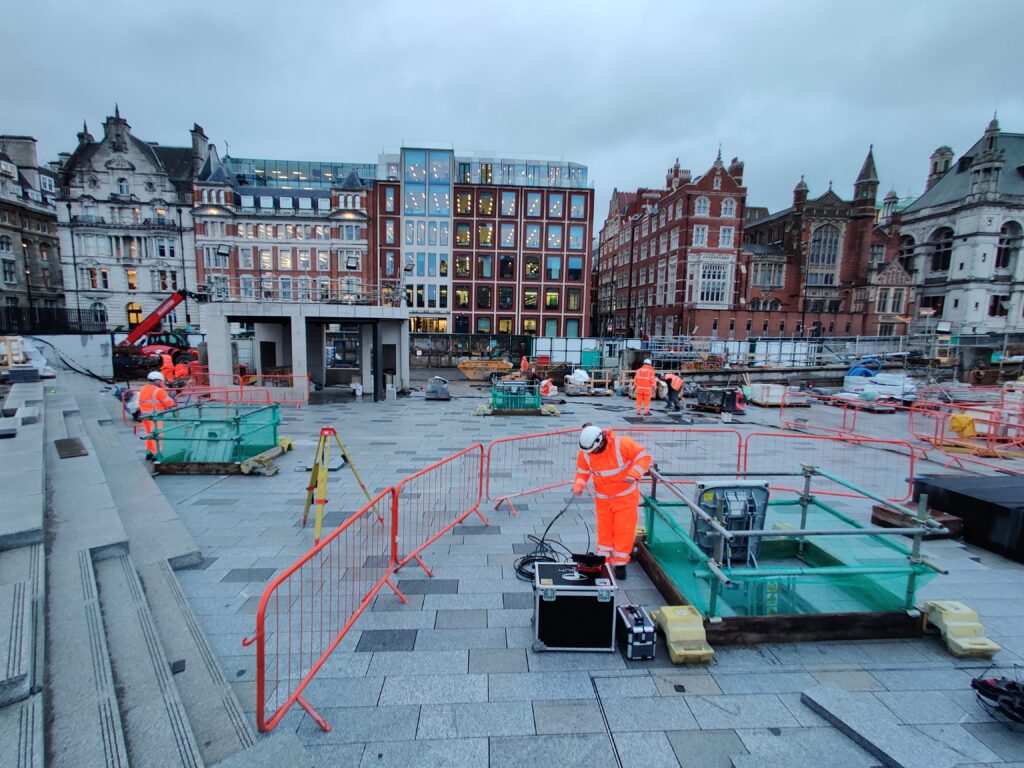
The Results
During the testing phase, the ATARI system navigated autonomously through the tunnel collecting detailed visual and 3D data. Abyss’s data pipeline was able to map all the data into a reality twin 3D representation of the tunnel. Its unique AI/ML analytics pipeline could then robustly identify various features and defects and localize them with high precision across the tunnel. The result is an accurate 3D reconstruction of the scene with all findings highlighted and tracked in an objective, accurate and scalable manner.
In summary, the system successfully identified all defects down to a size of 2cm, with location accuracy within 5cm, achieving a significant milestone in Abyss’s vision to pioneer autonomous systems for large-scale inspection.