P&ID Redlining
One of the largest leaseholders in the Gulf of Mexico prides itself on health and safety by dedicating time and resources to offshore asset integrity, risk reduction to creating and maintaining safe workplaces.
Offshore asset integrity requires updated documents for inspection and maintenance purposes. Generally, during project construction, the installation of assets and instrumentation are not fully congruent with the design drawings. The teams working on the platform also make changes to the equipment from time to time which can lead to discrepancies in the P&IDs and other data sets. Consequently, engineers planning the inspections and maintenance plans are not aware of the true condition of the complex process systems, and hence unable to meet all necessary safety and performance requirements.
Redlining is the process of highlighting, suggesting, and reviewing any changes in the technical drawing of the process plant. The redlining process in offshore platforms demands time, safety hazards, transportation costs, and considerable effort from the on-site inspectors. Using the Abyss Fabric’s digital twin with contextualized assets, the redlining activity can be performed from anywhere users have an internet connection. The time required to redline a complete platform using Abyss Fabric™ takes 3 to 4 weeks. The digital environment provided by the Abyss Fabric™ increases data coverage of assets in a short time; eliminates the health, safety, and environmental hazards encountered due to the personnel on board (POB), thereby significantly reducing the overall cost and carbon footprint.
When the customer in the Gulf of Mexico approached Abyss to assist with asset integrity efforts, the Abyss Fabric™ technology was able to produce a digital twin that provided them with visuals for every piece of equipment within the facility. The Abyss Asset Integrity Team (AIT) devised a redlining program to compare on-site data with the P&ID. Abyss AIT annotated the P&ID document and generated a register for the discrepancies observed between different data sets, such as as-built data, P&IDs, and CAD model. The location on P&ID is also identified with on-site imagery for every discrepancy.
Discrepancies between the two CAD models
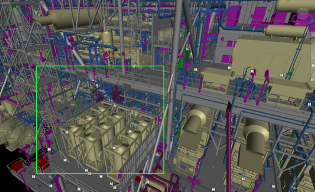
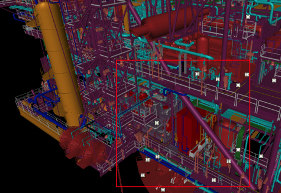
The discrepancies identified were further categorized into the following four groups/classes:
- Missing Elements On-site
- Missing Elements in P&ID
- CAD/P&ID Discrepancy
- Error in P&ID
A complete redlined P&ID document led to accurate baseline documentation for an effective inspection, NDT, and maintenance management system. Redlining established data reconciliation between the P&IDs, as-built data, and the PDMS model. The discrepancies identified in redlining helped the client to update the documentation and other relevant information in IDMS.
This particular customer was able to resolve the discrepancies in P&IDs identified by Abyss. Updated P&IDs aided in improved maintenance, inspection plans, and data management. As a case in point, during the redlining of this customer’s platform, P&ID was updated, and assets missing on-site were re-installed and fixed later by the maintenance team.
Since the customer was pleased with Abyss Fabric’s redlining process and results, they scheduled another redlining program for a second platform. A total of 566 discrepancies were reported. As a follow-up, the CAD model of the second platform was extensively updated by using contextualized Abyss Fabric™ and CAD/P&ID discrepancy register.